Here at Building Tall Research Centre at University of Toronto, we harness the power of machine intelligence and advances in robotics to design and implement innovative solutions for smart construction sites and facilities of near future.Unmanned aerial vehicles (UAV), also known as drones, are being increasingly used in the architectural, engineering, construction, and facility management (AEC/FM) industry [1]; The technological advances in the design and navigation of low-weight and autonomous UAVs have paved the way for their practical, robust, and cost-effective operation. In addition, these devices provide project team members with a reliable, safe, and fast access to a vast array of information regarding the construction of a tall building, some of which include construction progress and quality assessments, real-time site reports, and digital resources.
Under the supervision of Professor Brenda McCabe at Building Tall Research Group, construction automation researchers have embarked on an innovative study to facilitate automated monitoring of progress using off-the-shelf camera-equipped UAVs. In this research, a fully automated low-cost solution entitled “InPRO” [2] is being developed. InPRO facilitates projects’ timely and on-budget completions, and it employs autonomous intelligent UAVs (i.e., drones) to document and assess the construction progress using the robots’ on-board digital camera and sensors. The flying robots are given a route and instructed to inspect specific locations within the construction site. During the flight, high-quality images and videos are captured, accessible in real-time through the flying robots’ self-generated Wi-Fi networks. The images and videos are automatically processed using computer vision algorithms to detect objects and states of progress in the images [3,4,5]. The algorithms developed by Building Tall Research Group has achieved +90% and +95% accuracy rates in terms of object and state of progress detection respectively; these algorithms require no human intervention, drastically reducing the monitoring costs. Finally, the progress results are automatically incorporated into 4-dimensional (4D) building information models (BIMs) and construction schedules to better reflect the current conditions [6]. To communicate the state of progress between project team members, the building components can be color-coded in the project’s virtual models based on their performance (e.g., actual progress compared to expected progress). Below you can different stages of InPRO operation:
Automated Model-Driven Inspection Planning Support for Construction and Facility Management Applications
Before the inspection starts, an industry foundation classes (IFC)-based multi-dimensional BIM is provided to the system as input. The algorithms designed by our team automatically assess the data categories modeled within the IFC data model and extract the crucial information such as building element’s geometrics, schedule, and space information. A plan of the building floor is automatically generated based on the inspection date; using schedule data, the dynamics of construction environment is automatically taken into consideration. The user describes the inspection targets; for example, a team may be interested to inspect the doors on the second floor, or all objects that are behind schedule by 2 weeks. The program automatically retrieves the elements and performs automated inspection planning and optimization. This results in an information-rich plan for the UAVs which minimizes the resource use, maximizes the safety, and ensures complete data coverage and proper photo capture.
Interested to hear more? Please contact professor McCabe and the research staff at Building Tall for information on the relevant publications.
Automated Computer Vision-based State of Progress Detection for Indoor Environments
The application of computer vision techniques at indoor environments faces many challenges due to the highly cluttered indoor settings, occlusions, and more importantly the drastic changes in the view point and illumination patterns [1, 4]. The design of robust and low-cost vision techniques is vital to UAV-based progress tracking and ensures timely and accurate measurement of state of construction, facilitating situational awareness.
Researchers at Building Tall have designed a series of algorithms [2, 3, 4] that automatically detect the components of under-construction indoor partitions and their overall state of progress. For example, studs, insulation blankets, state of drywall work (plastered, painted, installed), and electrical outlets are automatically detected in the images without human intervention. The partition’s overall state of progress is also automatically detected with +95% accuracy rates.
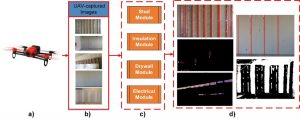
Building Tall researchers have been able to achieve 100% updating accuracy for 4D BIM updates [6]; this process can support real-time UAV-based progress tracking systems. For example, a full model update of a 3400 square-meter site can be performed in less than 2 minute. This is while manual model update for a single element can take a few minutes and is error prone; considering this on a building scale, the necessity for automated UAV-based systems such as InPRO [2] is more emphasized. The image below depicts and automatically updated 4D BIM of a construction site inspected by an off-the-shelf drone. Partitions color-coded in green, orange, and red are respectively on schedule, slightly behind schedule, and behind schedule [6].
“With the advent of new embedded sensing and internet of things (IoT), the future for the application of drones in AEC industry is brighter than ever”, explains Hesam Hamledari, a Building Tall researcher, “the smart construction sites of near future will be monitored by a network of connected drones which automatically coordinate the progress tracking work along with other tasks such as safety monitoring and productivity analysis. A wide range of sensors such as cameras, laser scanners, and RFID readers can be mounted on drones which make them a strong multi-sensory data collection platform”.
Our Latest Research Studies on Smart Inspection
If you are interested to hear more about other aspects of smart construction inspection, working papers, recent publications, and our current projects, please contact professor McCabe or the research staff at Building Tall Centre.
Relevant Publications:
[1] McCabe. B, Hamledari. H, Shahi. A, Zangeneh. P, Rezazadeh. E (2017). “Roles, Benefits, and Challenges of using UAVs for Indoor Construction Project Applications”, International Workshop on Computing in Civil Engineering 2017, Seattle, United States.
[2] Hamledari, Hesam (2016). “InPRO: Automated Indoor Construction Progress Monitoring Using Unmanned Aerial Vehicles”, Master of Applied Science Thesis, University of Toronto, Toronto, Canada, http://hdl.handle.net/1807/74735
[3] Hamledari. H, McCabe. B, Davari. S (2017), “Automated Computer Vision-based Detection of Components of Under-Construction Indoor Partitions”, Automation in Construction 74 (2017): 78-94. http://dx.doi.org/10.1016/j.autcon.2016.11.009
[4] Hamledari. H and McCabe. B (2016), “Automated Visual Recognition of Indoor Project-related Objects: Challenges and Solutions”, Construction Research Congress 2016, Puerto Rico. http://dx.doi.org/10.1061/9780784479827.256#sthash.DMa5xbIs.dpuf
[5] Hamledari. H, McCabe. B, Davari. S, Shahi. A, Rezazadeh. E (2017). “Evaluation of Computer Vision- and 4D BIM-based Construction Progress Tracking on UAV Platform”, International Construction Specialty Conference 2017, Vancouver, Canada.
[6] Hamledari. H, McCabe. B, Davari. S, Shahi. A (2017). “Automated Schedule and Progress Updating of IFC-based 4D BIMs”, ASCE Journal of Computing in Civil Engineering, http://dx.doi.org/10.1061/(ASCE)CP.1943-5487.0000660