Enabling the next generation of sustainable and resilient infrastructure
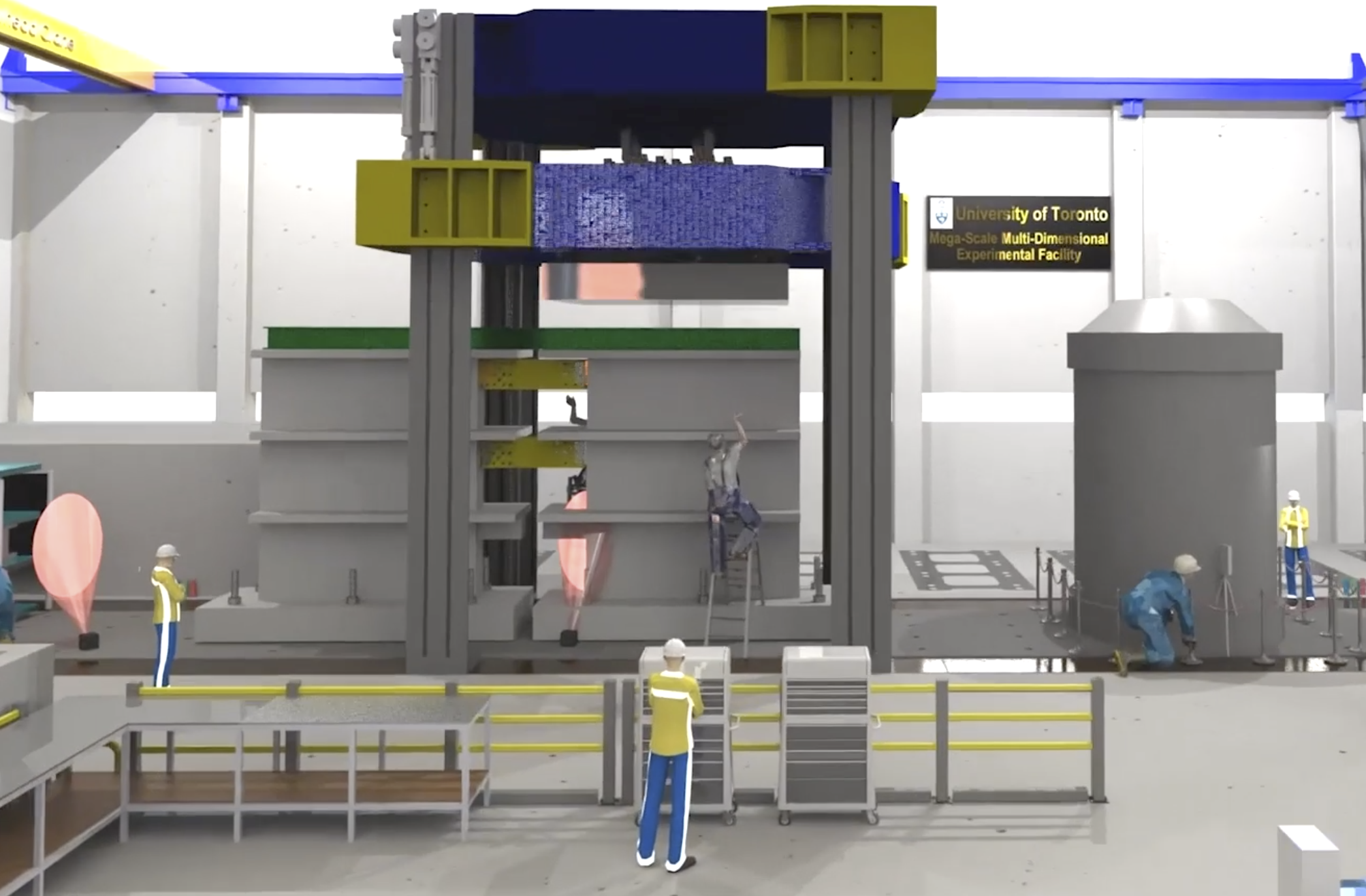
Building better and safer structures, such as high-rise buildings, bridges, dams, highways and even nuclear power plants, to withstand extreme conditions takes innovation and testing. An upgraded facility to simulate the forces of natural disasters on structures, such as earthquakes, tornadoes, hurricanes or tsunamis, is being constructed in the heart of Canada’s largest city.
Up until now, testing on building components has largely been done in a single axis while crushing, pulling or shearing specimens. The new installation is the world’s first fully adjustable multidirectional loading frame, known as the AMD (adjustable multidimensional) structural testing system. It’s a large-scale and large-capacity machine capable of simulating the complex effects of extreme loading events.
The future of structural testing is arriving within a (mostly) hidden venue at the University of Toronto where they routinely “break” very big things. Inside the Galbraith Building is the little-known, and seldom-seen, Structural Testing Facilities (STF), part of the Department of Civil & Mineral Engineering (CivMin). It’s the hangar-sized, three-storey tall, indoor laboratory where research is done by breaking full-size structural elements. Engineers call it “testing to failure” when a specimen fails under a load applied.
The Canadian construction industry, in partnership with academia, is innovating and developing this next generation of structural systems. Implementing new structural systems comes with risk and therefore large-scale, realistic multidimensional testing is the most efficient way to accelerate these innovations and allow for their implementation in real structures.
A new generation of infrastructure is needed to address sustainability and resilience challenges in the construction industry. This includes developing and implementing new structural systems that can withstand extreme loading conditions, like earthquakes and hurricanes, with minimal damage and quick recovery. “We use testing facilities to fail things in the labs in order to make sure they don’t fail in real structures,” says CivMin’s Professor Constantin Christopoulos. “In structural engineering, public safety is our number one guide in the work we do.”
Watch the introduction to the construction for our new AMD:
“Through the testing we’re planning to do with this new facility, we aim to enhance public safety by building safer structures,” says Christopoulos. “This is part of a major revamping of our entire labs, and this is part of the very big project funded by the Canada Foundation for Innovation by the Ontario Research Fund.”
Our testing centre is one of the pioneers in North America.
“Our testing centre is one of the pioneers in North America. We are bringing in a new piece of equipment called an AMD, which is short for adjustable multidimensional testing system. It will open up new horizons for researchers and industrial partners from all around the globe,” Armin Nassirnia, Manager of the STF.
In fact, the STF has a long history of testing involvement in many notable building projects, including the SkyDome (now Rogers Centre) and the CN Tower. The process of testing building elements to failure in the STF has resulted in advancements to building codes in Canada and beyond.
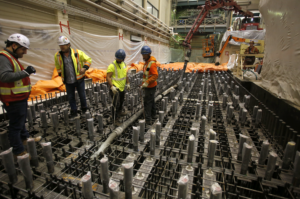
“We’re looking to minimize damage sustained and will allow an area, a city – sometimes even an entire country – to bounce back much quicker after a major catastrophic event.” To do this kind of research requires full-size building components, “Large-scale testing is the golden standard,” explains Christopoulos. It removes the uncertainty of testing from smaller scale models and extrapolating the data, which can lead to inaccuracies.”
The new AMD will allow testing of specimens of up to 27 m in length and 7.5 m in height, along with multiple anchor points to stage multiple specimens for successive testing.
The path to construction first began with moving equipment in March 2022, cleanup of the space in May 2022 and then demolition. Large testing equipment, such as the old Baldwin Press, was removed entirely to clear the way while the Shell Element Tester was moved across the lab floor and wrapped up to protect it. The existing strong floor, in use since 1960, had to be demolished to a depth of about two metres.
Demolition of the heavily reinforced concrete strong floor required the use of heavy equipment, hoisted into position using the lab’s built-in crane. At times, two backhoes were in place with jackhammers equipped to speed the effort.
Once the previous strong floor section was fully removed, new construction of the steel anchor system began. With over 90 tonnes of steel structure and rebar in place, the first pour of concrete in May 2023 saw 35 concrete trucks arrive for the overnight endeavour.
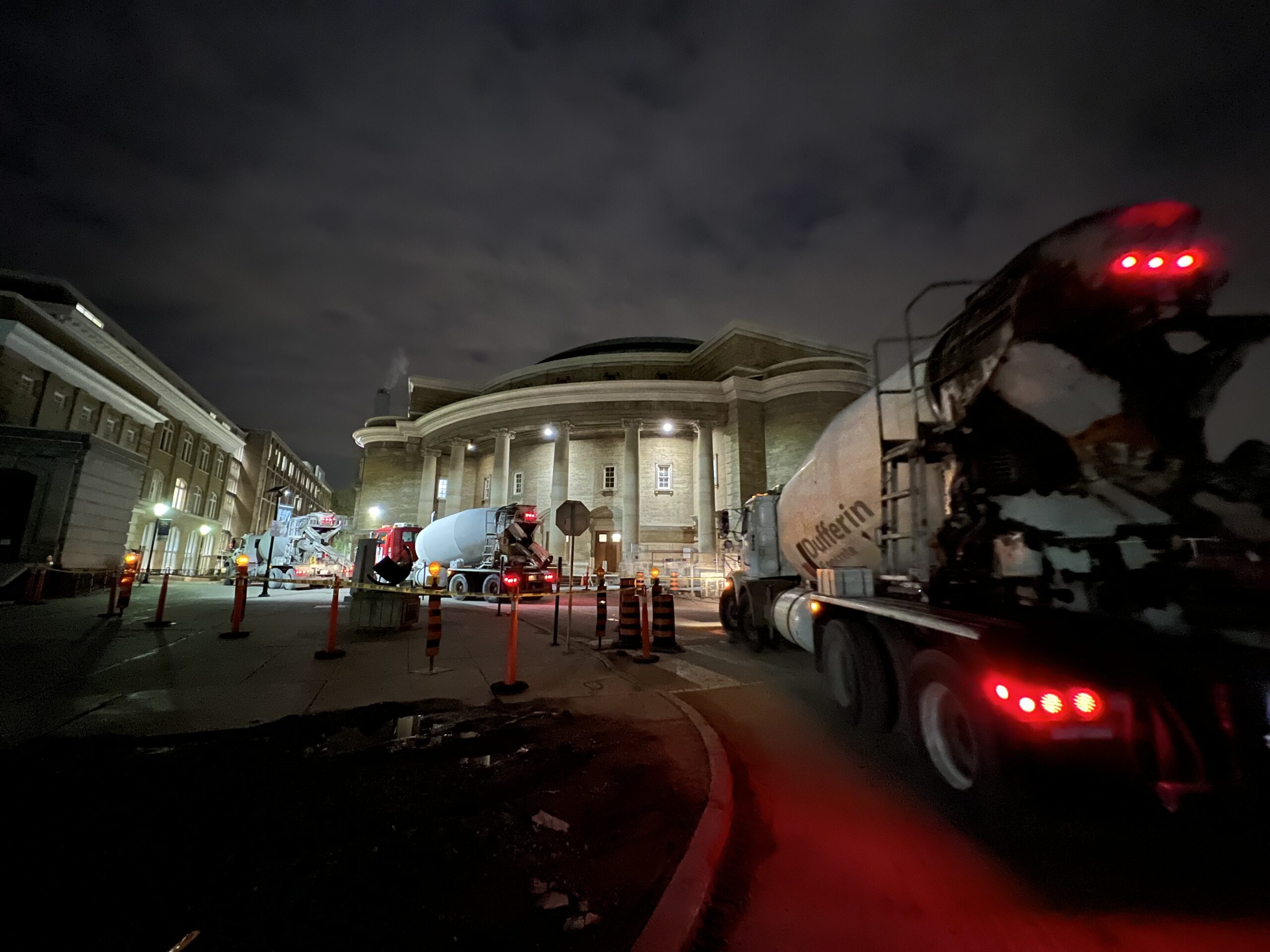
Now, with about three-quarters of the concrete in place, the rest of the strong floor is nearly completed and awaiting a final pour to bring it level with the rest of the existing deck.
Over time, much can change from the original concept and proposal. In the intervening years since first proposed, the world has experience a worldwide pandemic, supply chain issues, currency fluctuations, inflation and more. This has necessitated making up for unforeseen hurdles not imagined a decade ago. As such, components for the AMD are being sought from new sources Europe in an effort to find the ideal technological and economic fit for the project.
Project partners include CivMin Professors Oh-Sung Kwon, Evan Bentz, Oya Mercan and Jeffrey Packer. The team is also collaborating with a team of structural engineering and large-scale testing experts at other leading North American facilities to develop, commission and use this unique equipment.
“We observe the way components fail, in order to understand their behaviour,” says Christopoulos summing up what researchers accomplish in the STF. “We really do love to break things here.”
by Phill Snel
Funding and collaboration opportunities
CivMin is seeking funding and industry collaboration to complete the AMD project.
If interested, please contact Liz Petrova, Associate Director, Development for Engineering Advancement via email: elizabeth.petrova@utoronto.ca
By the numbers
- 35 concrete trucks for the first pour of the strong floor (about 75 per cent of total)
- over 90 tonnes of steel rebar and reinforcement
- 100-tonne tension capacity per anchor point in the strong floor. AMD has four footings that will be mounted to the strong floor through a
- 48 anchor points in the strong floor
- adjustable testing stations horizontally and vertically for various specimens
- static and dynamic testing as well as hybrid testing,
- capacity: up to 1600-tonne vertically, and up to 400-tonne horizontally
- AMD length 6 x 6.8 m
- AMD height 8.6 m
- six degrees of freedom for AMD: forward/back, up/down, left/right, yaw, pitch, roll.
- AMD can provide force up to 1600-tonne vertically, and up to 400-tonne horizontally
- 27 m maximum length for testing
- 7.5 m maximum height for testing
- 8x distributed fibre optic sensors embedded for strain measurement
- 168 square metres of new strong floor lab space
- 336 cubic metres of strong floor built